Adobe PDF
(2.84 MB)
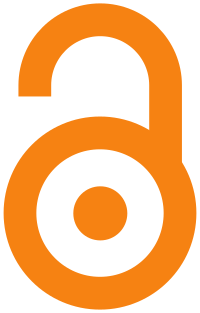
Page view(s)
118
checked on May 2, 2024
Download(s)
135
checked on May 2, 2024
